Advanced Deepwater Monitoring
We conduct research in new methods to improve deepwater monitoring and address installation of advanced sensors on βalready deployedβ risers, flowlines, trees, and other deepwater devices in collaboration with Astro Technology and the Clear Gulf Project.
The research is part of the Clear Gulf Joint-Industry Project (JIP) that forms a collboration between Astro Technology, NASA, and various oil and gas companies. This partnership utilizes the test facilities and expertise of NASA for operating in remote environments and under harsh conditions. The objective of this collaboration is to jointly develop technology that minimizes impact on the environment, improves safety, and monitors critical energy infrastructure. A new area of application is the retrofitting of existing subsea structures with fiber optic monitoring sensors installed by divers or Remotely Operated Vehicles (ROVs).
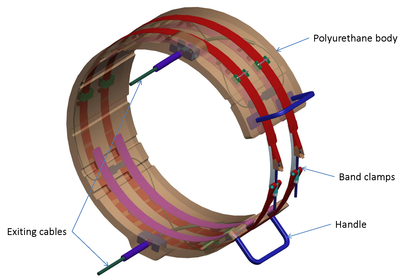
Benefits of Deepwater Monitoring
- Monitor fatigue life on risers and flowlines by detecting Vortex Induced Vibration (VIV)
- Maintain flow assurance of oil and gas transport pipelines
- Meet regulatory reporting requirements and insurance qualifications
- Visualize data from remote locations
- Provide soft sensing by consolidating data streams into actionable information
- Advanced control of upstream systems
Dynamic constraints may change constantly. Two of the most recent projects are
- Tendon strain monitoring for Tension Leg Platforms (TLPs)1
- Monitoring of deepwater flowline operating conditions to avoid hydrate formation2
Advanced monitoring and control is performed with the APMonitor Optimization Suite for analyzing large-scale and complex systems such as these subsea structures.
Offshore Platforms
TLPs (Tension Leg Platforms) are floating oil production platforms that are used for drilling and production operations in deepwater environments, such as the Gulf of Mexico. TLPs are designed to be stable and resistant to the forces of wind, waves, and currents, and are well-suited for use in deepwater environments where these forces can be significant. TLPs consist of a floating platform supported by a series of tendons, which are long, flexible cables anchored to the sea floor. The tendons are kept under tension, which helps to keep the platform stable and upright. TLPs are typically designed with a triangular or square base, which provides a large area for drilling and production operations.
There are several other designs for platforms used for offshore oil and gas production, drilling, and wind energy. These include semi-submersibles, compliant towers, and spars. Each platform design has unique characteristics and is suited for different types of environments and applications.
Semi-submersibles are platforms that are partially submerged in water, with most of the platform above the waterline. They are supported by a series of pontoons, which provide buoyancy and stability. Semi-submersibles are well-suited for use in areas with moderate to high wave and current activity, as they are able to move with the waves and currents to maintain a stable position. However, they are not as stable as other types of floating structures and may be more susceptible to structural damage or failure in severe weather conditions.
Compliant towers are platforms that are supported by a single, flexible tower that is anchored to the sea floor. They are designed to be compliant, meaning that they are able to move and bend with the forces of wind, waves, and currents. Compliant towers are well-suited for use in areas with high wind and wave activity, as they are able to withstand these forces without significant structural damage. However, they may not be as stable as other types and may require additional ballast or weight to maintain a stable position.
Spars are platforms that are supported by a single, cylindrical column that is anchored to the sea floor. They are designed to be lightweight and streamlined, which makes them well-suited for use in areas with high current and wave activity. Spars are also able to withstand significant wind loads and are able to maintain a stable position in severe weather conditions. However, they are not as versatile as other designs and are limited in terms of the types of drilling and production operations that can be performed on them.
Other types of floating oil production platforms for deepwater production include Floating Production, Storage, and Offloading (FPSO) vessels, which are ships that are converted to be used for drilling and production operations, and Floating Drilling Units (FDUs), which are specialized drilling platforms that are designed for use in deepwater environments. Both FPSOs and FDUs have the advantage of being able to move to different locations and can be used in a variety of different environments. However, they may not be as stable or resistant to the forces of wind, waves, and currents as TLPs and may be more susceptible to structural damage or failure in severe weather conditions.
References
- Hedengren, J.D., Brower, D.V., Kidder, K., Hillman, Z., Data-Driven TLP Tendon Loads from Internal Hull Fiber-Optic Sensors, ASME 42nd International Conference on Ocean, Offshore and Arctic Engineering, OMAE2023/103309, Melbourne, Australia, June 2023. Preprint | Video | Presentation
- Hedengren, J.D., Brower, D.V., Wilson J.C., High, G., Witherow, K., New Flow Assurance System With High Speed Subsea Fiber Optic Monitoring Of Pressure And Temperature, ASME 37th International Conference on Ocean, Offshore and Arctic Engineering, OMAE2018/78079, Madrid, Spain, June 2018. Preprint
- Brower, D.V., Seaman, C., Bentley, N.L., Tang, H.H., Kipp, R.M., Wilson, J.C., Le, S.Q., Hedengren, J.D., Full-Scale Testing of a Friction-Based, Post-Installable, Fiber-Optic Strain Sensor for Subsea Monitoring Systems, Topic: 4-6 Innovative Technologies for Deepwater Low-Cost Production, Symposium 4 Pipelines, Risers, and Subsea Systems, ASME 37th International Conference on Ocean, Offshore and Arctic Engineering, OMAE2018/77117, Madrid, Spain, June 2018.
- Eaton, A., Safdarnejad, S.M., Hedengren, J.D., Moffat, K., Hubbell, C., Brower, D.V., Brower, A.D., Post-Installed Fiber Optic Pressure Sensors on Subsea Production Risers for Severe Slugging Control, ASME 34th International Conference on Ocean, Offshore and Arctic Engineering, OMAE2014-42196, St. John's, Newfoundland, Canada, June 2015. Preprint
- Seaman, C., Brower, D.V., Le, S., Tang, H., Development and Testing of a Post-Installable Deepwater Monitoring System Using Fiber-Optic Sensors, ASME 34th International Conference on Ocean, Offshore and Arctic Engineering, OMAE2015-41305, St. John's, Newfoundland, Canada, June 2015. Preprint
- Asgharzadeh Shishavan, R., Brower, D.V., Hedengren, J.D., Brower, A.D., New Advances in Post-Installed Subsea Monitoring Systems for Structural and Flow Assurance Evaluation, ASME 33rd International Conference on Ocean, Offshore and Arctic Engineering, OMAE2014/24300, San Francisco, CA, June 2014. Presentation and Preprint
- Brower, D.V., Brower, A.D., Hedengren, J.D., Asgharzadeh Shishavan, R., A Post-Installed Subsea Monitoring System for Structural and Flow Assurance Evaluation, Offshore Technology Conference, OTC 25368, Houston, TX, May 2014. Preprint
- Brower, D., Hedengren, J.D., Asgharzadeh Shishavan, R., and Brower, A., Advanced Deepwater Monitoring System, ASME 32st International Conference on Ocean, Offshore and Arctic Engineering, OMAE2013/10920, Nantes, France, June 2013, ISBN: 978-0-7918-5531-7. Preprint Presentation
- Brower, D., Hedengren, J.D., Loegering, C., Brower, A., Witherow, K., and Winter, K., Fiber Optic Monitoring of Subsea Equipment, OMAE 2012, Rio de Janiero, Brazil, Volume 1: Offshore Technology, Number: 84143, pp. 769-776, June 2012. Preprint | Presentation